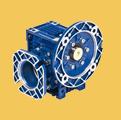
Gear Box
To check the oil in your Gear Box, drain out a small sample and check it for sludge, water, or metal. Replace any seal with oil leakage around it. Check the oil level and replace it if necessary. Make sure all hardware is tight and in good working condition. Check that the outside of the case is free from excessive deposits. The backlash can be checked by rotating the pinion shaft back and forth and, before the gear teeth engage fully, noting the amount of free rotation. The endplay can be checked by noting the amount of movement in the Gear Box output shaft when pulling up and down on a fan blade tip. While some backlash and endplay are necessary for proper gear life, excessive backlash and endplay mean it is time to replace the Gear Box. When in doubt, contact a qualified service contractor.
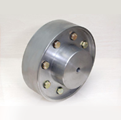
Drive Shaft and Couplings
Use an approved method, like an optical device or dial indicator, to check the alignment of your drive shafts and Couplings. Look for signs of corrosion or other damage on the tube, especially near welding. Check the connections between the flex elements and the tube. Check the connections between the Coupling Halves and the Motor and Gear Box shafts. Carefully inspect the metallic flex elements for evidence of corrosion or fatigue. Inspect the elastomeric flex elements for cracks, brittleness, or other signs of wear. If your Drive Shaft has more than one span, check the mid-span bearing carefully and lubricate as necessary. Be sure to check the alignment of both shafts and ensure that the bearing hold-down hardware is in good working condition and tight. If replacement of a component of a two-shaft system is necessary, look into replacing the entire system with a single span shaft. This will dramatically reduce maintenance costs.
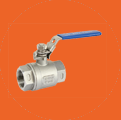
Valves
Manually operate the float switch or valve to ensure that it is opening and closing properly.
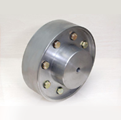
Fans
Check to be sure that the bushing and its hardware are in good condition and that the fan bushing is tight on the motor shaft. Check the joints between the support and its motor mount. Look for erosion or corrosion on the blades, especially near welds and between the end plates and blades. Check the tightness and condition of the hub as well as the bushings between the hub and shaft. Propeller fans are either fixed-pitch or adjustable-pitch. Fixed-pitch propeller fans have welded or riveted connections between the blades and the hub. Check these blades for erosion or corrosion. Carefully inspect the connections between the hub and the blades. Check the tightness and condition of the bushing between the hub and shaft. Adjustable-pitch propeller fans have bolted connections between the blades and the hub and some means of readjusting the blade pitch angle. Check these blades for signs of erosion, corrosion, or excessive buildup of deposits. Carefully measure the pitch angle of each blade. Readjust the blades within 1-2° of manufacturer’s recommended pitch angle. Check the condition and tightness of the hardware attaching the hub to the blades. If there is a hub cover, examine the connections between it and the fan hub. Check the overall condition of the fan cylinder material, especially all welds in steel shrouds. Check the tightness and condition of all the assembly and hold-down hardware. Examine adjoining segments for any leaks. Using the longest fan blade, measure the fan blade tip clearance around the cylinder. You can adjust tip clearance by adjusting the support or cylinder according to manufacturer’s instructions.
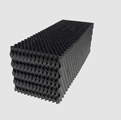
Fill Media
Make sure the Fill Media is not sagging horizontally, which causes water to run to the lowest point instead of distributing evenly. This sagging allows for easier air passage in areas with less water. Fill Media which is spaced too far apart also doesn’t break up water efficiently. Fill Media in poor condition reduces your performance by 30 or 40%.

Mechanical Supports
Check all bolted connections between the structure itself and the support on fiberglass and steel towers. Look for evidence of evidence of iron rot wherever the support contacts the structure on wood towers. Examine all steel components for loss of metal or corrosion, especially near bearing surfaces and welds. Check the tightness of the connections between the support and the mechanical equipment and between the support and the tower structure. Check all bolted connections in the support itself for proper condition of hardware and tightness.